702 Hoses for FMG’s Iron Bridge Magnetite Project
We’re pleased to have supported the FMG Iron Bridge Magnetite Project, supplying super flexible Slurryflex mining hose for the new ore processing plant.
Client
FMG Client Logo
Year 2021
Commodity type Iron ore
Location WA
Application Gravity circuit
Hoses built 702
Turnaround time 22 weeks
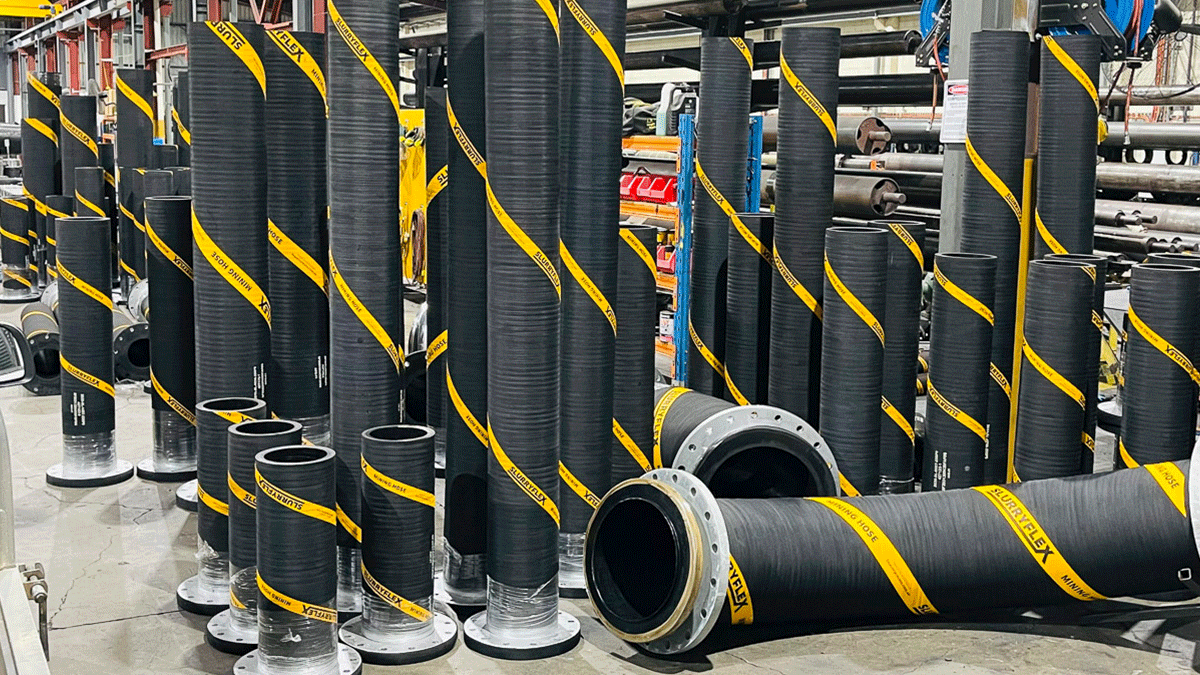
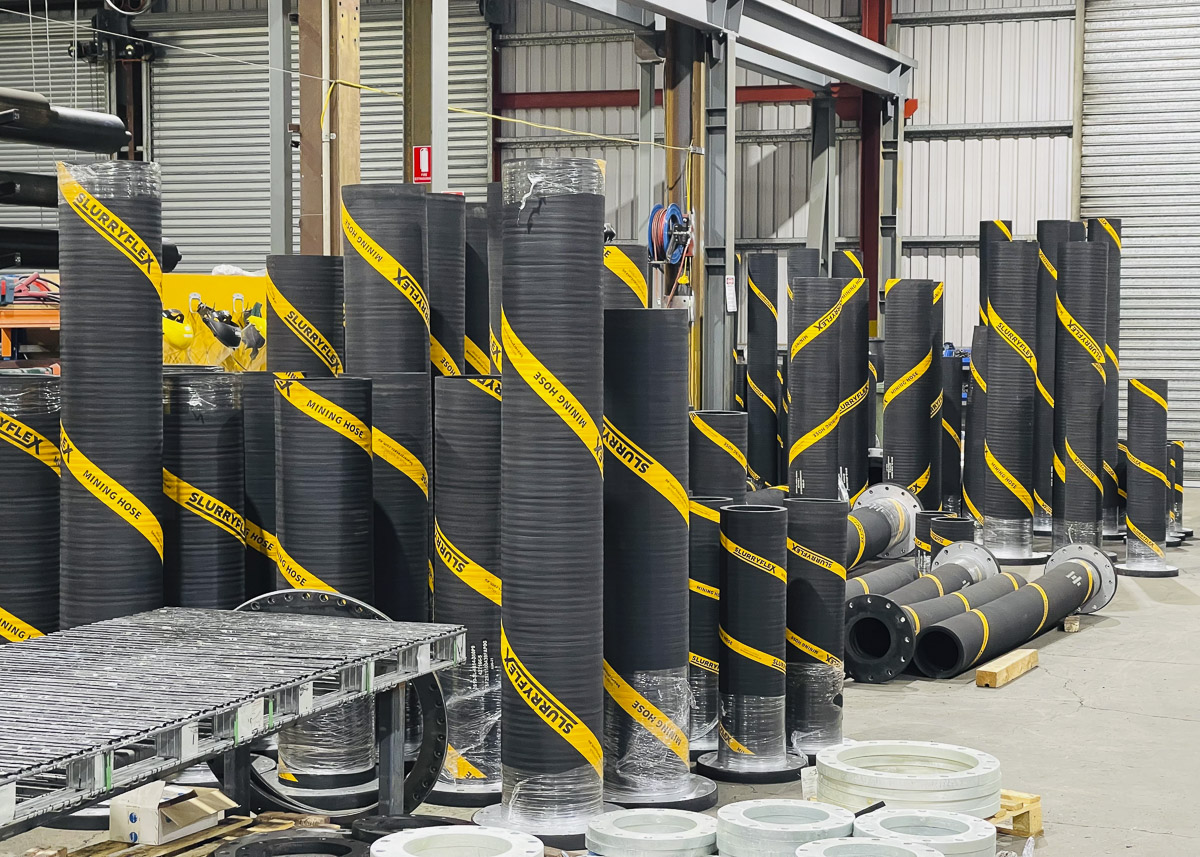
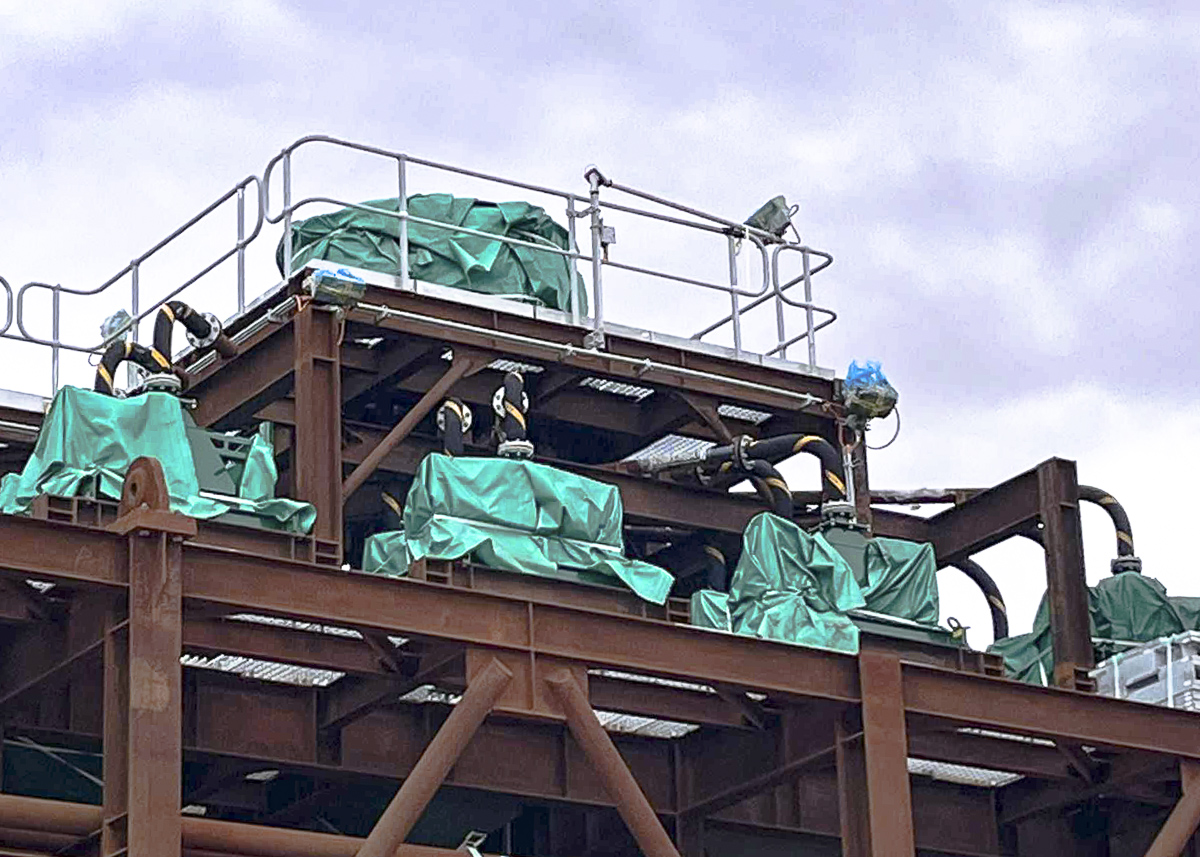
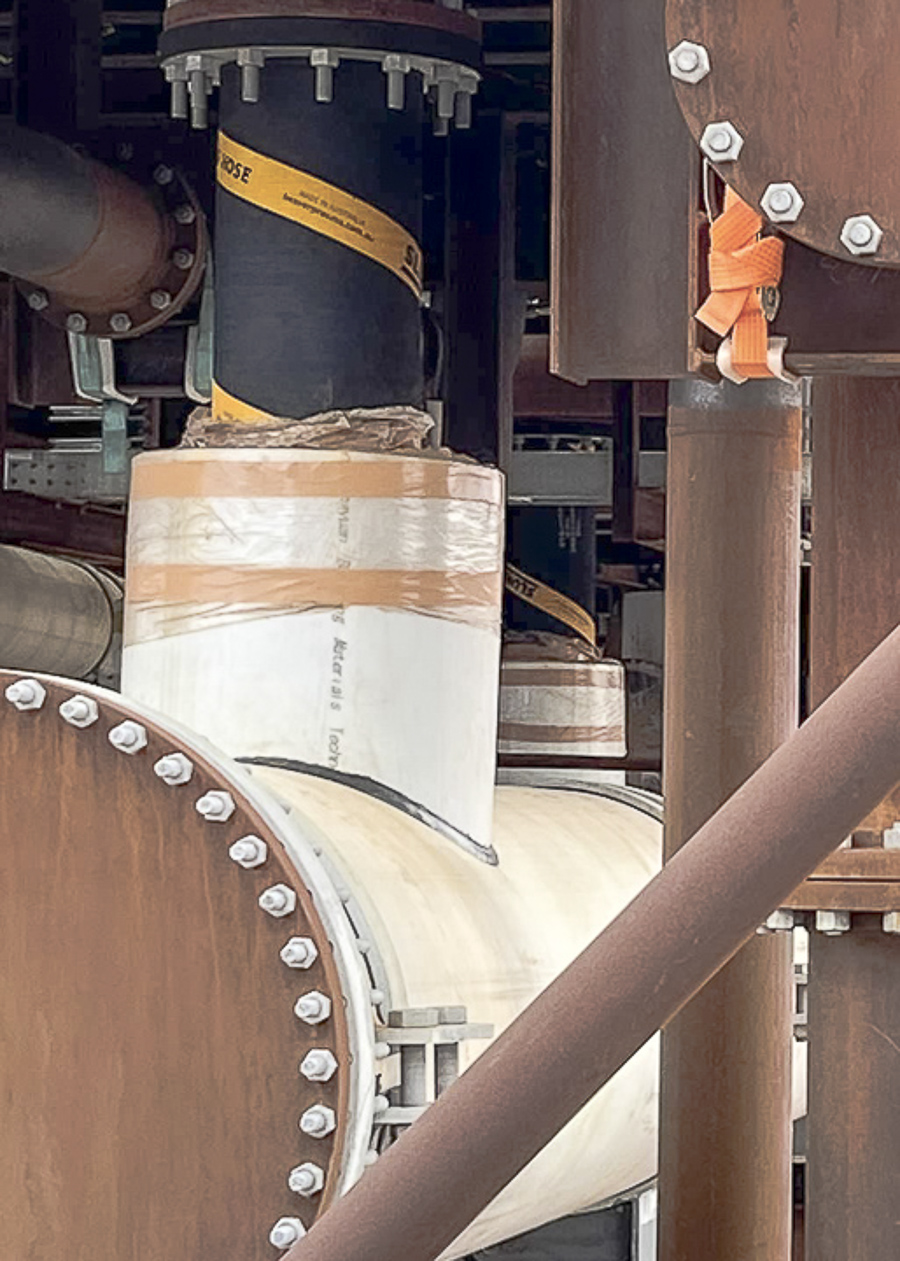
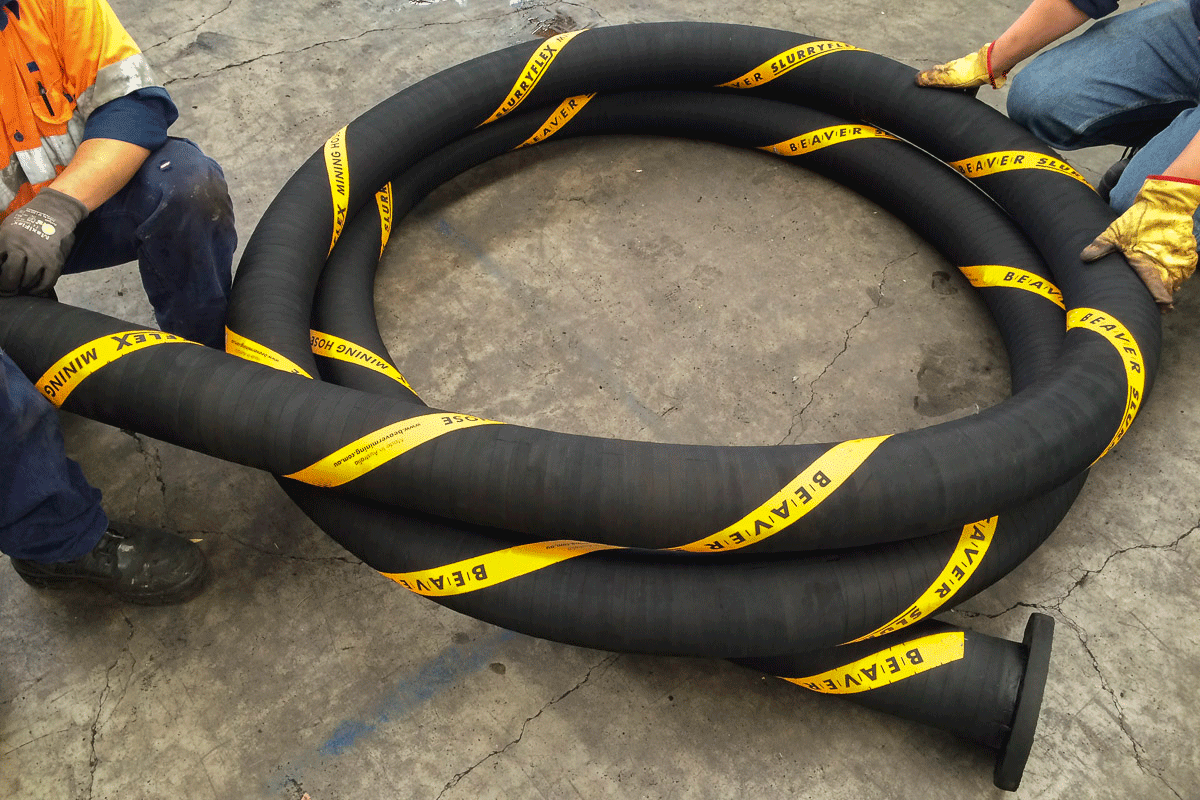
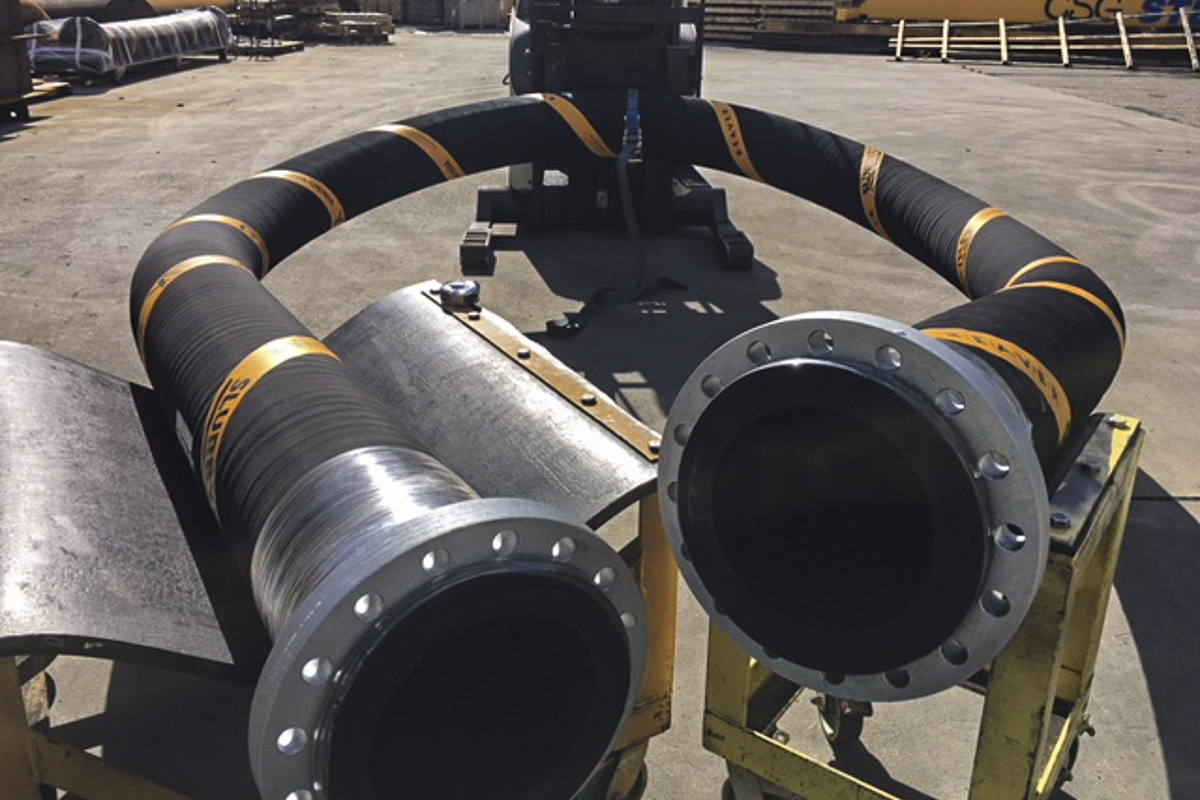
We worked with design engineer Hatch to define the piping specification for the gravity circuit.
FMG needed a flexible mining hose to cope with significant thermal movement from the HDPE gravity launder pipe—up to 420mm of movement in operation.
The engineers at Hatch, who designed the piping system, said rigid pipe was an automatic ‘no’ because it wasn’t flexible enough. And most hoses they looked at weren’t suitable because they kink.
That’s why all the hoses on the new plant are SF-Series Superflex—it’s the only hard wall slurry hose available that can reach a bend radius of 4-7D.
And it will withstand severe wear from the coarse, sharp iron ore slurry.
Our Brisbane manufacturing team built 702 hoses for the project over a period of 22 weeks—more than 8,000 hours work—and delivered them to site on schedule ready for installation.
Related projects
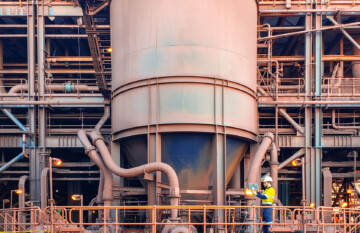
How Roy Hill Solved Costly Unplanned Piping Maintenance for Good
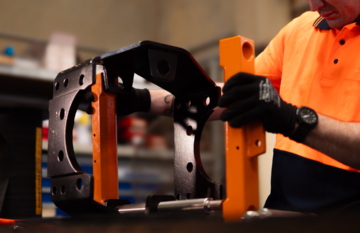
WA Lithium Mine get 12x Longer Wear Life in Slurry Control Valves
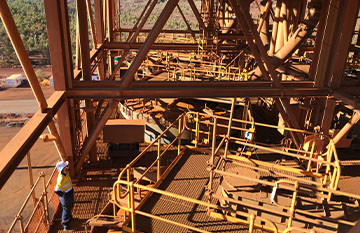
8x Longer Lifespan for Cyclone Overflow Piping at FMG Solomon Mine
We're here to help
Got questions? Need advice? Tap into our experience and get specialist advice from our friendly team.
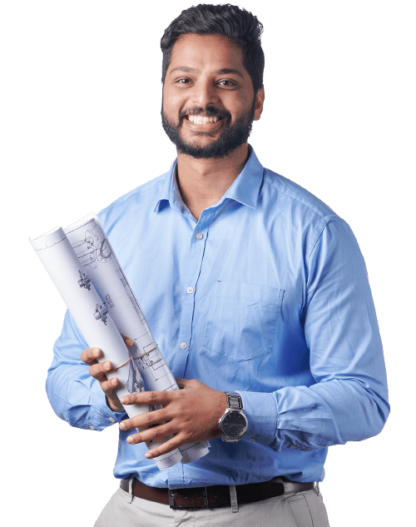

Slurry piping audits
Solve slurry piping maintenance problems for good. No more leaking pipes, no more unplanned shutdowns.