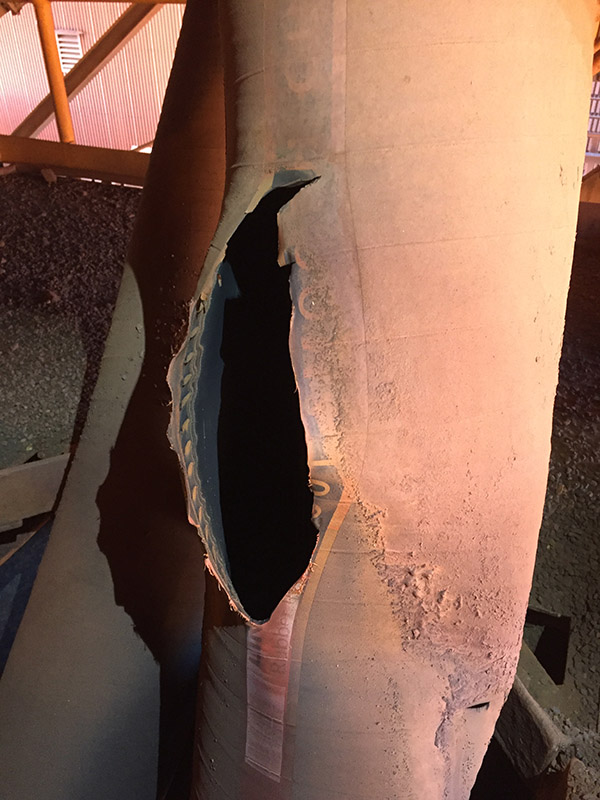
Cyclone piping challenges
Back in 2018, the maintenance team at Rio Tinto’s Tom Price iron ore mine were only getting 12 weeks out of standard mining hose on the cyclone feed clusters.
It was a massive undertaking to shut each section and replace the hoses. Plant performance was slipping so they wanted to see if there was a better option.
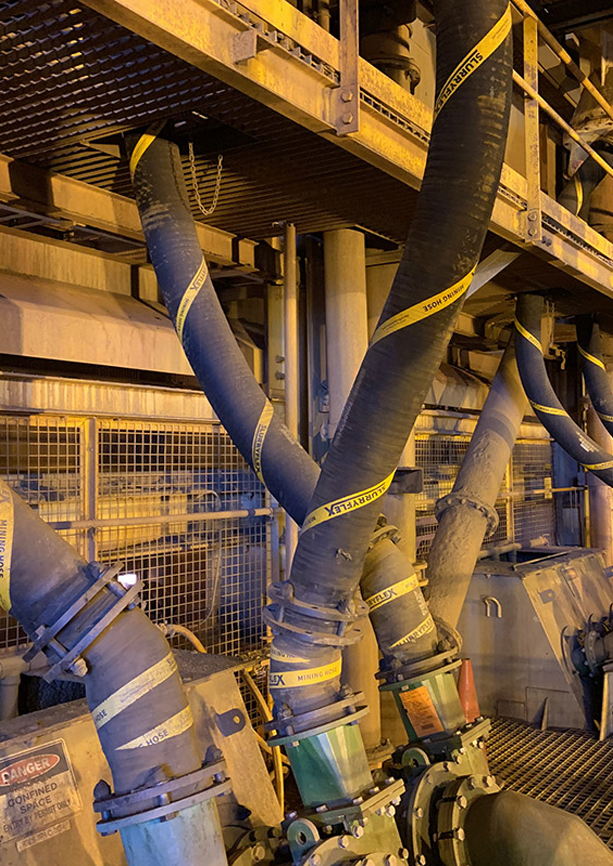
Piping redesign
After reviewing the system and talking to the team, we recommended redesigning the hoses to improve performance.
Our recommendations
- Resolve kinking – we modified the dimensions of the hoses to stop kinking and splitting.
- Standardise the dimensions – having hoses all the same length means they can quickly swap one out for a spare. No more hazardous muff couplings or downtime waiting for replacements and easier cataloguing.
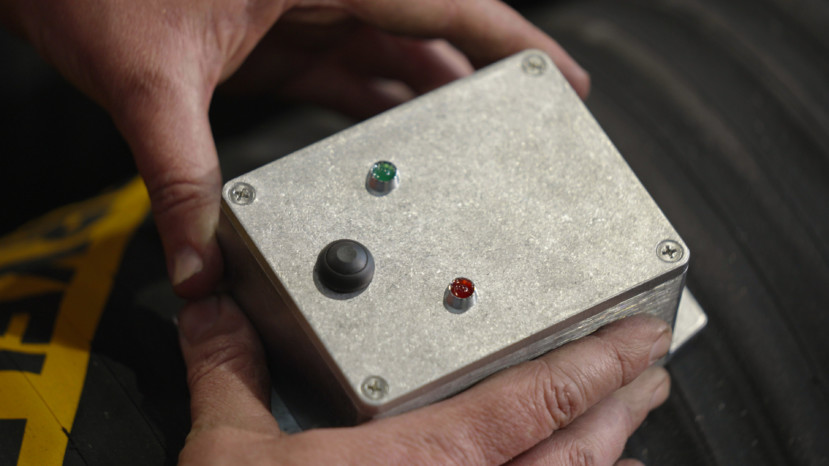
3. Predict wear – adding in wear monitors on the hoses helps the team keep track on when they need to replace the hose.
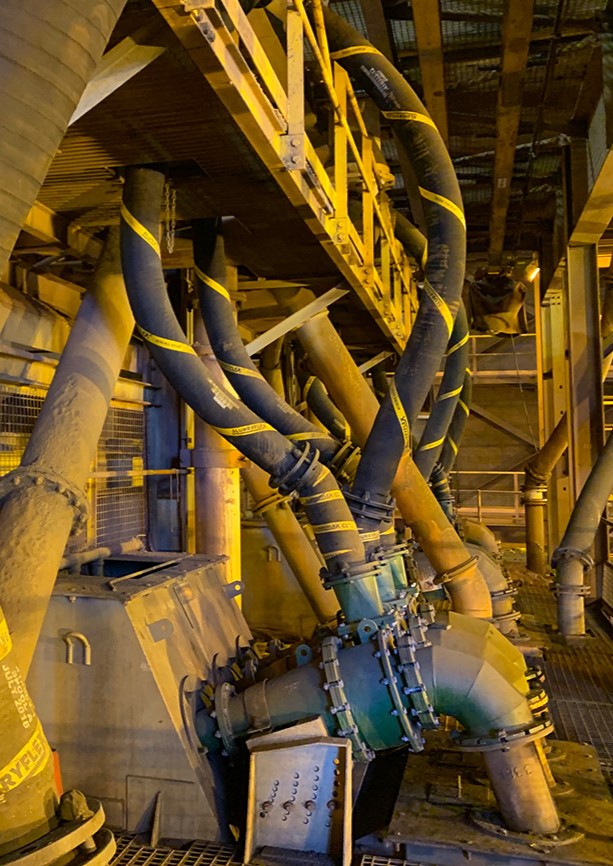
The team agreed it was the right approach, so we got to work building the new DN150 Slurryflex mining hoses in our Brisbane factory.
The result?
The team have increased their shutdown intervals from twelve weeks to thirty six weeks.
That’s three times the wear life.
And not a split or bandaged hose in sight.
Make your process plant piping work for you – not the other way around.