Choosing the right lined piping system for your plant is so important. There are many different options out there, and you might not be an expert in all of them. The last thing you need is for the piping you’ve just installed to fail early and impact your production targets.
So, we’ve compared the most common types of lined and unlined pipe used in processing plants to help you understand all the options that are now available:
- Unlined steel
- Unlined HDPE
- Rubber-lined
- Polyurethane-lined
- Ceramic-lined
- Alumina ceramic-lined
- Basalt-lined
Unlined Pipe
The two main unlined piping options used in mineral processing plants are unlined carbon steel and high-density polyethylene (HDPE).
Steel
Unlined carbon steel pipe is a cheaper option than lined pipe and wears better than HDPE. Unlike most lined options, you can weld, repair, or modify the piping on site as needed.
The biggest problem with unlined steel is its poor corrosion resistance. It will also fail quickly—often within weeks—if used for highly abrasive applications.
✔ Can be repaired or modified onsite
✔ Longer wearing than HDPE
✖ Poor corrosion resistance
✖ Poor wear resistance
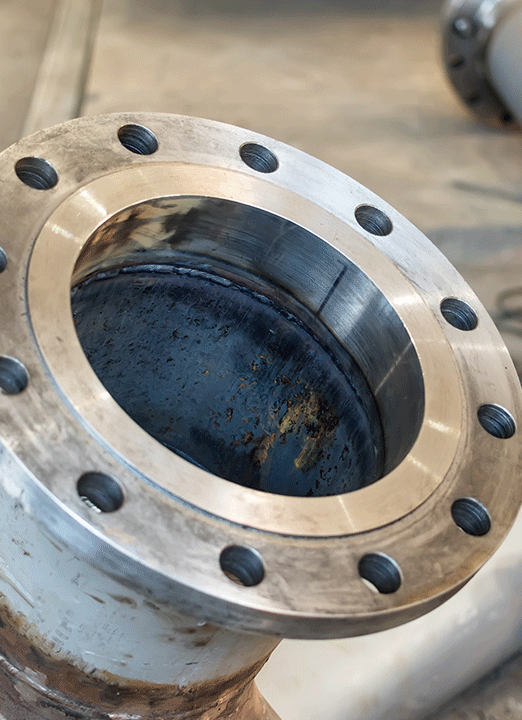
Unlined steel
HDPE
HDPE is an economical option for low wear, corrosive applications, such as process water. Like unlined steel, you can also weld and modify it on site.
The downside is that HDPE wears very quickly in processing plants, particularly with abrasive applications like iron ore and coal.
You also need to watch out for pressure ratings and temperature conditions. HDPE has a maximum pressure rating of 25 bar at 20°C pipe temperature. As it heats up, it loses its strength and pressure rating, which can cause blowouts and failures.
✔ Can be repaired or modified onsite
✔ Good corrosion resistance
✖ Fast wearing
✖ Loses strength in high temperature and pressure systems
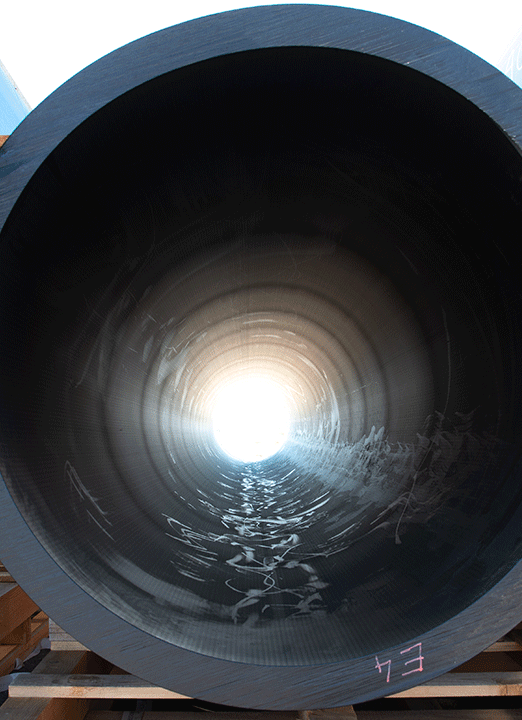
HDPE
Lined Pipe
Rubber
Traditionally, the default option for high-wear applications has been rubber-lined steel. Good quality rubber lining absorbs and disperses particle impact and provides good wear resistance.
Rubber lining is manufactured in two ways—cold bonded or hot vulcanised.
With cold bonded rubber lining, the pipe interior is blasted and primed, then cured rubber sheets are glued to the pipe interior. The advantage of cold bonded lining is that it can be repaired or replaced on site.
In the hot vulcanised process, uncured rubber is glued to the pipe substrate and vulcanised in a steam autoclave. The process provides a stronger bond between the lining and the substrate versus the cold bonded option.
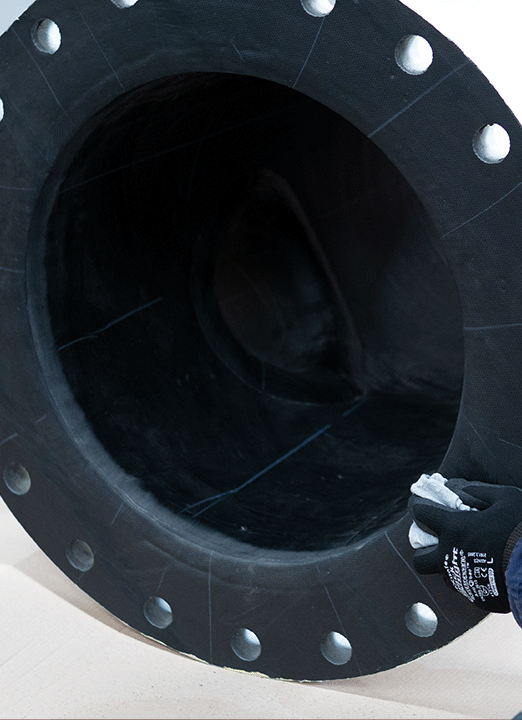
Fixed flange rubber-lined pipe
Rubber lining provides good wear resistance but has some drawbacks. It has high surface roughness, with high friction loss, which means more pumping energy is required.
If you go with a natural rubber lining, it has an operating temperature of -45 to 95°C. Synthetic rubber liners—such as EPDM or nitrile rubber—will give you a higher temperature tolerance but can be more expensive and wear faster.
The manufacturing process can affect how well the rubber wears. If the lining is hand glued and moulded to the pipe substrate, this increases the potential defect rate.
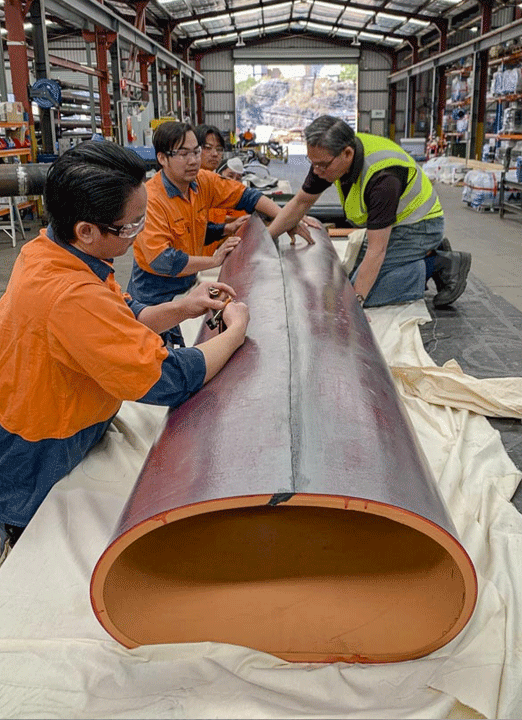
Rubber-lined pipe manufacturing
Rubber lining that’s poorly manufactured has high spots in the liner, bubbling where it hasn’t been glued properly, or gouging and lifting at the leading edge. Once this wear starts, it can cause the entire lining to suck off the pipe wall and into the pump.
Rubber lining has further manufacturing limitations which customers should be aware of.
It can only be manufactured in lengths of 6 metres, which can work in process plants, but it makes rubber-lined steel unsuitable for pipelines.
Being a manual process, it’s also slow to produce. This is something to consider if you are working to tight lead times.
✔ Quality rubber will provide good wear performance
✔ Suitable for hard rock applications
✔ Cold bonded liner can be field repaired or replaced
✖ High friction loss
✖ Poor resistance to hydrocarbons and high temperatures
✖ Manufacturing processes increase defect rate and production time
Polyurethane
High-performance polyurethane resists gouging from high-energy particles, unlike rubber liners that lack the wear resistance needed for abrasive slurry. This makes it an ideal choice for sharp-particle slurry applications like coal, and large-particle applications like oil sands, dredging, and hard rock.
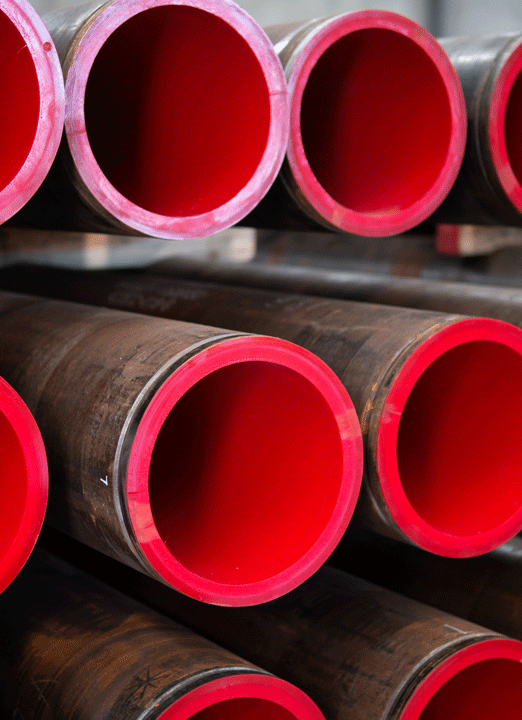
High-performance polyurethane lining
Polyurethane is a cast liner, so it’s bonded to the pipe and spun cast to give an exact internal diameter. This process allows you to increase the lining thicknesses to match internal diameters of other pipework, or use non-standard pipe diameters.
In addition to withstanding erosive wear, the liner is chemically compatible with most fluids and isn’t affected by dissolved oxygen and reagents. Standard liner formulations have temperature limits of 0 to 60°C, but you can modify the formulation for special applications outside the range.
It’s important to note that not all polyurethane lining is equal. If the manufacturer uses the wrong formula, doesn’t mix it properly, or doesn’t apply it correctly, you can end up with bubbling, poor adhesion to the steel substrate, and a liner that simply won’t last.
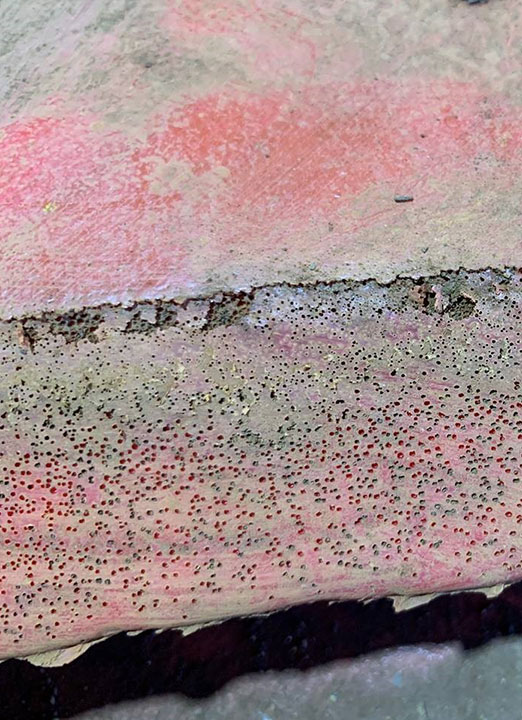
Example of poor-quality polyurethane liner
This photo was taken from an iron ore mine in the Pilbara. You can see how porous this poor-quality polyurethane liner was. It began leaking soon after they installed it. So it’s worthwhile to do your research into how the product is made, and check that the manufacturer is ISO 9001 accredited.
✔ Excellent wear performance
✔ Suitable for aggressive wear applications
✔ Low friction loss
✔ Reagent compatibility
✔ Resistance to dissolved oxygen
✔ Available in 18m lengths
✖ Standard formulations have temperature limitations
✖ Quality can vary across suppliers
✖ Can’t be modified or repaired in-situ on site
Ceramic
Ceramic liners are used in processing plants where there’s high wear and high temperature. There are three main types of ceramic liners used in processing plants—alumina ceramic liners, ceramic epoxy, and basalt. Ceramic liners are used extensively in coal, gold, hard rock, and iron ore due to their wear resistance.
Alumina Ceramic
Alumina ceramic linings are very wear resistant, particularly to sliding wear abrasion. They’re excellent for coal processing plants and other aggressive applications.
The two types of alumina ceramic linings are tiles or cylinders. Tile pads are glued or grouted to the wall of the pipe, while cylinders are pre-formed and glued, or grouted into the pipe. Both are then put through a furnace to bond the ceramic liner to the substrate.
You might experience two common problems with hard-wearing materials like ceramics: shattering and debonding. Shattering happens when high-velocity particles hit the lining. Debonding occurs when slurry gets into the grout and forces the tile off the wall. You’ll find this on poorly manufactured ceramic tile liners.
✔ Highly resistant to abrasive wear
✔ Suitable for hard rock applications
✔ Cold bonded liner can be field repaired or replaced
✖ Can shatter with high velocity particle impact
✖ Quality can vary, causing tile debonding
✖ Length limit of 6m
✖ Heavier than other lined piping systems
Basalt
Basalt is a low grade, more economical ceramic. It’s often used in coal wash plants due to its high and low temperature resistance, as well as excellent abrasion, corrosion, and chemical wear. The liner is made from basalt rock and crystallising agents, which are melted and hot poured into moulds or centrifugally cast. The liner is then glued into straights or lobster back bends. The liner is generally 20mm thick so it can be very heavy compared to other liner types.
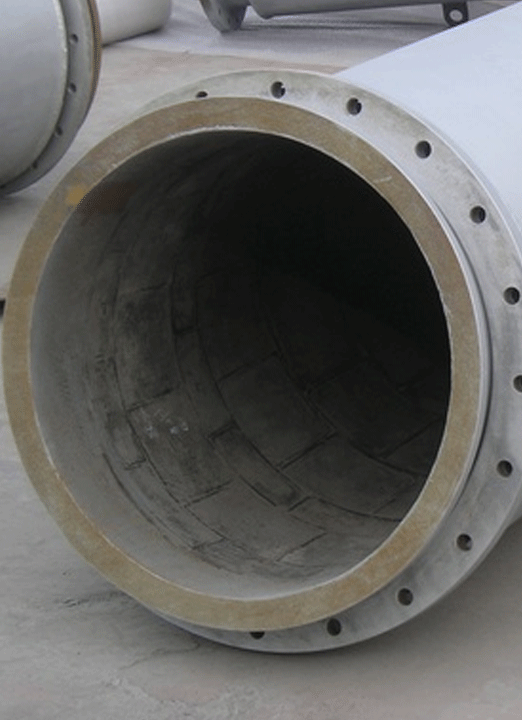
Basalt lining
The downside of basalt liner is that it doesn’t wear as well as alumina ceramics, particularly in high-velocity applications with large particles. It has a maximum internal pressure rating of 10 bar but is best suited for applications of 7 bar or lower.
✔ Economical liner
✔ High temperature rating
✔ Resistant to abrasion, corrosion and chemical wear
✖ Least wear-resistant ceramic liner type
✖ Not suitable for high pressure applications
✖ Very heavy compared to other liner types
The right liner will make your job easier
In our experience, processing plants are often designed and built with piping that is lower in cost and fails quickly. Over time, piping continues to be replaced with what’s been ordered in the past and this may not be durable enough. This leads to halts in production and unplanned maintenance—both of which are preventable.
Choosing the right lined piping for your slurry type and plant conditions will give you a significantly better system. The right piping will last the distance to your scheduled shutdowns, reduce your unplanned maintenance, and make your plant more efficient.