If you use mining hose in your mineral processing plant, you may be interested to hear what goes into making one. Did you know that mining hose is built from the inside out? Or that during vulcanisation the rubber turns into a semi-liquid?
In this article, we go into detail on the different layers of a mining hose, how they are built, and how they work to provide you with flexible and durable piping in your plant.
A mining hose has three layers:
- Inner tube
- Reinforcement layer
- Outer protective layer
1. Inner tube
The first step in building a mining hose is to wind the inner layer onto the mandrel to form the inner tube with a specified thickness. This first layer acts as the wear liner and is in direct contact with the slurry or process fluid.
Mining hose is built from the inside out, which lets you match the internal diameter (ID) of the hose to any size, or bore match to suit other components in your plant. This means you’re not limited to a specific pipe size or liner thickness.
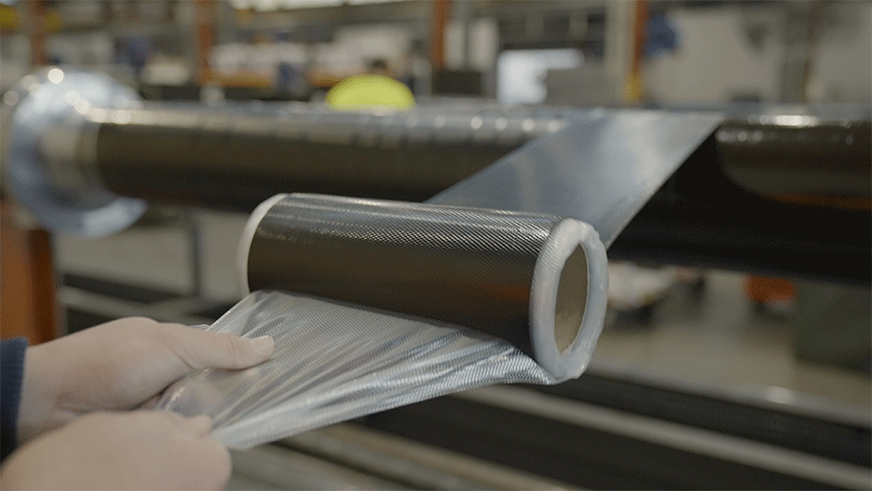
Wrapping inner layer on the mandrel
The inner tube layer offers two key benefits. First, it’s a durable layer that resists abrasion and wear. Second, it can be customised to handle a range of chemicals. If the slurry type is highly abrasive but chemically neutral, typically the liner will be a natural rubber. For extreme or severe wear, a more resilient option like a ceramic tile liner is more suitable.
If you’re dealing with slurry that contains hydrocarbons (such as oil sands, copper, or base metal flotation plants that use diesel and fatty acids in the flotation process), you’ll need to consider synthetic rubbers. Examples of these include hydrogenated nitrile, chlorosulfonated polyethylene, or bromobutyl.
2. Reinforcement layer
On top of the inner tube, the hose builder winds a rubber-skimmed polyester fabric (also known as bedding rubber) around the length of the hose. The bedding rubber gives the hose its structural integrity.
For hard-wall or suction hoses, they then coil a high-tensile steel wire helix in between layers of bedding rubber. This helix stops the hose from being sucked flat in suction.
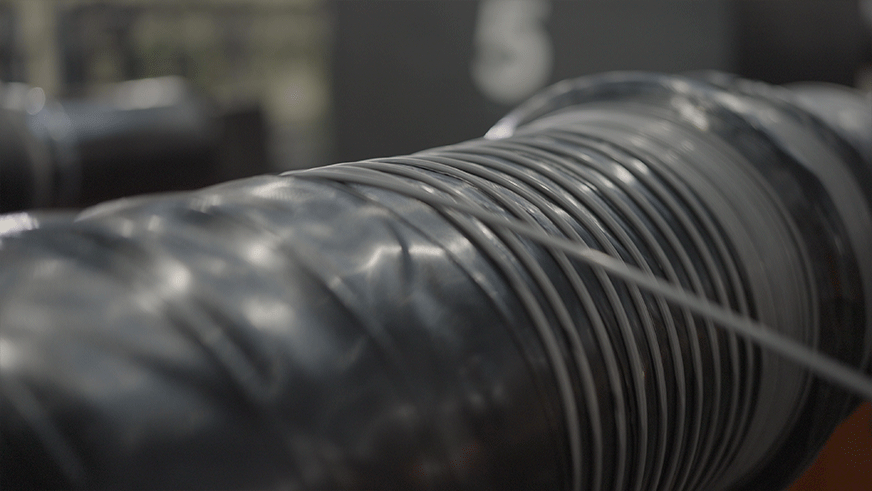
High tensile steel wire coil
During this step, the hose builder creates the end connections, and builds the integral flange connections into the hose. The end flange is pre-lined with rubber and the hose layers are taken up and over the spigot.
With high-pressure hoses, the wire helix is wound over the top of the spigot to firmly hold it in place.
3. Outer layer
The outer layer is made of a rubber impregnate, or a rubber-coated fabric, that is resistant to harsh weathering and UV exposure. This layer is difficult to puncture if the hose is accidentally hit by a vehicle or other mining equipment.
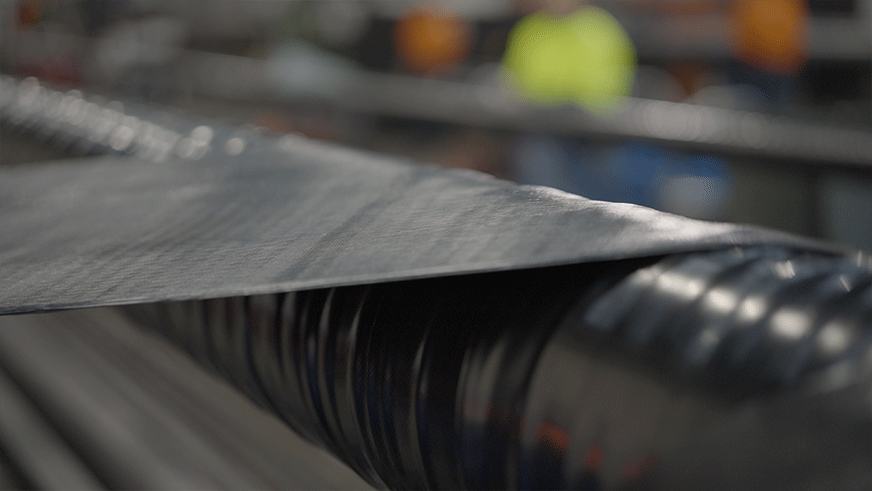
Outer protective layer
Natural rubber is one of the best materials for the outer layer, but there are rubber compounds that give increased resistance to extreme weather, chemicals, and oils. For example, synthetic rubber is flame retardant and abrasion resistant.
The final step in the manufacturing process is vulcanisation. As hoses are manufactured from uncured rubber, they need to be cured in an autoclave. This involves cooking the mining hose in a high-temperature and steam-pressure atmosphere to bond the layers of the hose together. Depending on the hose size, thickness and rubbers used, this can take anywhere from three to eight hours.
During the vulcanisation process, as the rubber turns into a semi-liquid, it flows and bonds together. Then, it turns from multiple layers of product into a single integral product. This process eliminates air bubbles or separation between the wire helix and bedding fabric in hard-wall hoses, making it stronger and harder wearing.
Selecting a quality hose
There are so many different elements that go into making a quality mining hose. The raw materials and manufacturing process play a key role in creating a product that is both reliable and durable.
If you’re installing mining hose in your processing plant, it’s handy to know how it’s made. This way you can make more informed choices when it comes to selecting a hose that is up to whatever challenges you throw at it.